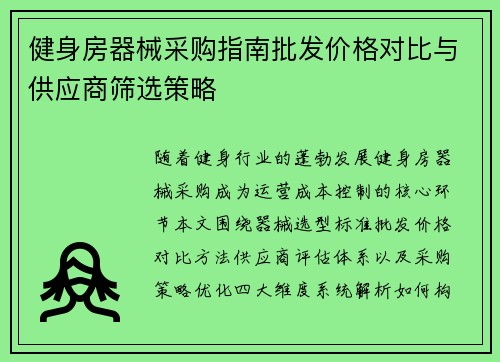
健身器材制造的碳中和路径与可持续发展实践
- 13
随着全球气候问题加剧,碳中和成为制造业转型的核心议题。健身器材行业作为传统高能耗领域,正面临从材料、生产到回收的全链条减排挑战。本文从材料革新、清洁生产、循环体系、责任协同四个维度,系统剖析行业碳中和路径。通过可再生材料替代、零碳工厂建设、产品全生命周期管理及多方利益相关者合作,探索可持续发展实践。文章结合技术创新与商业模式变革,为健身器材企业提供兼具环境效益与经济价值的转型方案。
1、材料革新路径
传统健身器材以钢铁和工程塑料为主,其生产过程的碳排放占产品总碳足迹的62%。采用再生钢材可减少45%的能源消耗,如美国某品牌已实现90%杠铃片使用废钢重塑技术。生物基复合材料正在突破强度瓶颈,德国企业研发的竹纤维复合跑步机底盘,较传统材料减碳38%且具备天然抑菌特性。
材料轻量化带来双重减排效益,铝合金替代方案使椭圆机骨架重量降低30%,运输环节燃油消耗减少15%。日本厂商开发的蜂窝结构填充技术,在保持器械强度的同时减少20%原材料使用。材料创新需兼顾性能与成本,目前碳纤维回收技术突破使高端器材改造成本下降40%。
供应链协同创新成为关键,国内某企业与高校共建材料实验室,开发出可降解橡胶地垫材料,使用寿命结束后可转化为有机肥料。这种闭环设计使产品碳足迹降低52%,开辟健身器材环保新赛道。
2、清洁生产转型
生产环节占健身器材总碳排放的28%,能源结构转型势在必行。山东某工厂屋顶光伏覆盖率已达85%,配合储能系统实现生产用电60%自给。德国企业将锻压余热回收用于注塑工序,使每台器械制造能耗降低12.7千瓦时。
数字化制造技术大幅提升能效,浙江企业引入AI驱动的智能冲压系统,材料利用率从78%提升至93%。物联网监测设备实时优化喷涂车间VOC处理能耗,使单位产品污染治理成本下降40%。美国厂商应用的3D打印拓扑优化技术,减少支撑结构材料浪费达65%。
零碳工厂认证推动系统变革,台湾地区某企业通过制程热能梯级利用、碳捕捉设备安装,成为全球首个获得DNV零碳认证的健身器材工厂。其经验显示,清洁生产改造可使单厂年减排1.2万吨CO₂。
3、循环体系构建
产品生命周期延长是减排关键,瑞典品牌推出的模块化力量训练架,通过部件替换可实现15年超长使用周期。法国企业开发的智能健身镜采用易拆解设计,维修率提升30%的同时,回收材料再利用率达91%。
逆向物流网络建设成效显著,美国连锁健身房与制造商共建回收平台,每年处理2.3万吨退役设备。拆解后的钢材直接回炉,塑料部件经化学分解再生为新原料。这种模式使单车类器材碳足迹降低37%,并创造新利润增长点。
服务化商业模式正在兴起,荷兰企业推行的"健身即服务"模式,用户按月付费使用器材,企业负责维护更新。该模式使产品周转率提高4倍,单台设备服务周期内减排1.8吨CO₂。共享健身仓采用物联网定位技术,设备利用率提升至76%。
星空体育官方网站4、责任协同网络
行业标准建设加速转型进程,ISO发布的健身器材碳足迹核算指南,统一了从原材料开采到报废处理的核算边界。欧盟新规要求2026年起进口器械须提供碳标签,倒逼供应链深度减排。我国发布的团体标准将回收材料占比要求提升至30%。
产学研合作突破技术瓶颈,中科院团队研发的废旧橡胶低温裂解技术,使瑜伽垫回收产物纯度达99%。校企共建的智能拆解机器人实验室,处理效率较人工提升20倍。产业联盟组织的碳中和技术路演,已促成47项专利转化。
消费者教育重塑市场生态,碳积分奖励计划使38%用户选择环保器材。某APP通过运动数据兑换植树额度,累计中和器械使用碳排放1200吨。品牌碳标签认知度调查显示,72%采购商将碳指标纳入供应商评估体系。
总结:
健身器材制造业的碳中和转型,本质是价值链的重构与生态的重塑。从生物基材料应用、可再生能源驱动、产品服务化创新到产业协同网络,每个环节都蕴含技术突破与模式变革机遇。实践表明,领先企业通过全链条减排可获得5-8%的成本优势,同时提升品牌溢价15%以上。
未来行业发展将呈现"四化"趋势:材料生物化、生产智能化、服务场景化、责任可视化。随着碳关税政策实施和消费者意识觉醒,建立覆盖研发、制造、消费、回收的负碳体系,将成为企业核心竞争力。这场绿色革命不仅关乎环境保护,更是重塑产业格局的战略契机。